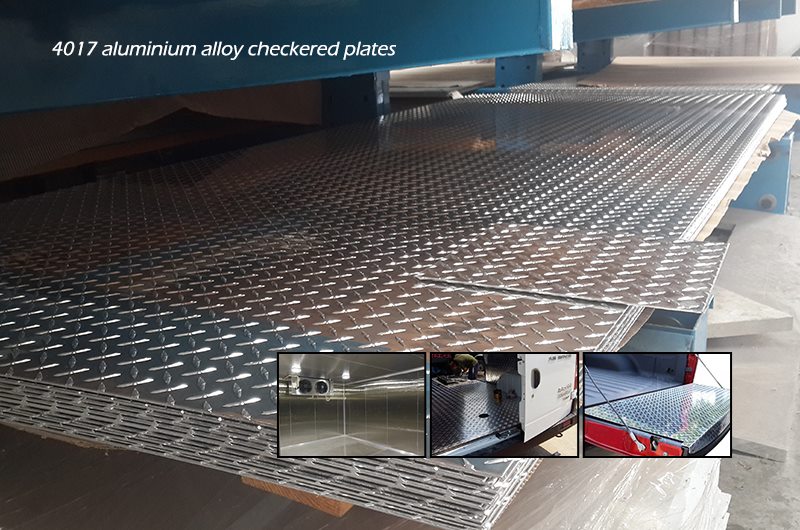
4017-H2X state aluminum alloy checker plate and preparation method thereof, the 4017-H2X state aluminum alloy checker plate has a certain hardness, good wear resistance, no naked cracks after 90° bending, no orange peel texture, and fine surface , Can be painted, suitable for building materials and manufacturing decorative parts, such as transportation, building floors, truck compartments, cold storage, elevators and other anti-skid plates and screen skeletons and other packaging and decorative materials.
4017-H2X state aluminum alloy checker plate is characterized in that, it is composed of the following raw materials by weight percentage: Si0.6~1.6%, Fe≤0.7%, Cu 0.1~0.5%, Mn 0.6~1.2%, Mg 0.1~0.5% , Zn≤0.2%, other single impurities <0.05%, total impurities <0.15%, and the balance is Al;
The preparation method of 4017-H2X state aluminum alloy pattern plate, comprises the following steps:
Step 1: batching according to the composition of the raw materials and smelting and casting;
Step 2: Soaking the ingot, machining the milling surface;
Step 3: hot-rolling to a hot-rolled billet with a thickness of 6.0-10.0 mm;
Step 4: Cold-rolling and billeting: cold-rolling and billeting the hot-rolled billet, and cold-rolling the billet with a total reduction of not less than 40%, the rolling thickness is 2.1mm to 5.1mm, and the cold rolling rolling oil The refractive index is greater than 90%, and the kinematic viscosity value at 40℃ is 2.2~2.4mm²/s;
Step 5: cold rolling and embossing: use patterned rollers to perform cold rolling and embossing with a processing rate of 20% to 50%, and the cold rolling and embossing speed is 70 to 180 m/min;
Step 6: Continuous annealing: The embossed patterned plate strip is cleaned, and then rapidly annealed in a continuous annealing furnace. The temperature of the continuous annealing furnace is set between 350 ° C and 410 ‘C, and the strip running speed is set at 2 ~8 m/min, water-cooled, dried, straightened and rolled after being baked;
Step 7: Tensile straightening or cross-cutting: The continuously annealed aluminum alloy checkered plate is drawn and straightened or cross-cut into corresponding coils or sheets.