Status: H14
Composite layer (%): 8~12
Thickness (mm): 0.085~0.15
Tolerance (mm): ±0.005
Tensile strength σb (MPa): 180~220
Elongation δ (%): ≥0.5
Yield strength σ0.2 (MPa:) ≥ 145
Main use: fins
The 4343/3003/4343 aluminum alloy brazing foils for heat exchangers were produced by hot-rolling composite process. The coating ratio, microstructure and mechanical properties of aluminum alloy brazing foils were studied by optical microscope, electron tensile testing machine and scanning electron microscope. performance. The results show that the thickness of 4343 aluminum alloy cladding layer of 4343/3003/4343 aluminum alloy brazing foil is uniform and the composite interface is smooth. The tensile strength, yield strength and elongation of the brazing foil are 116.6 MPa, 58.7 MPa and 40.3%, respectively.
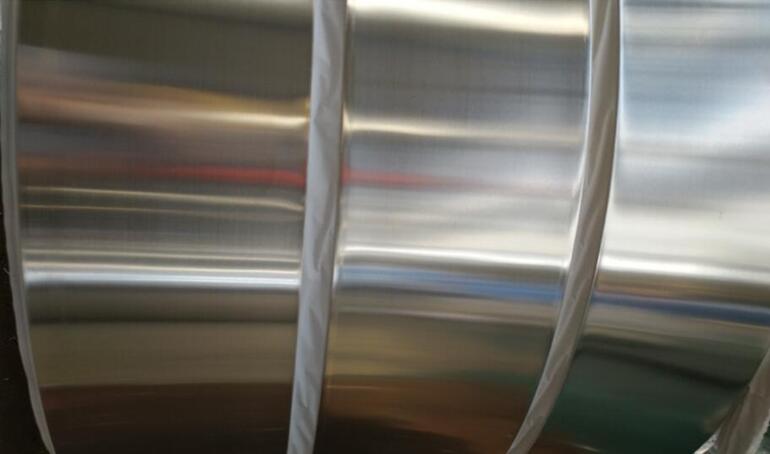
The three-layer aluminum alloy composite foil has good thermal conductivity, corrosion resistance and brazing performance, and is widely used in heat exchange systems such as engine radiators, intercoolers, and air conditioner condensers in automobiles [1]. 4343/3003/4343 three-layer aluminum alloy composite foil in stock is the most typical and most widely used aluminum heat transfer material. The outer layer of 4343 aluminum alloy is called skin material, which is a hypoeutectic Al-Si alloy with a melting point of 590-610℃ , is a brazing material for connecting composite pipes, composite plates and composite fins; the inner layer of 3003 aluminum alloy is called the core material, which is an Al-Mn alloy with certain strength and corrosion resistance, and is the bearing capacity of the heat exchange system part